Das Design von Oxis Energy verspricht herausragende Energiedichte, Herstellbarkeit und Sicherheit
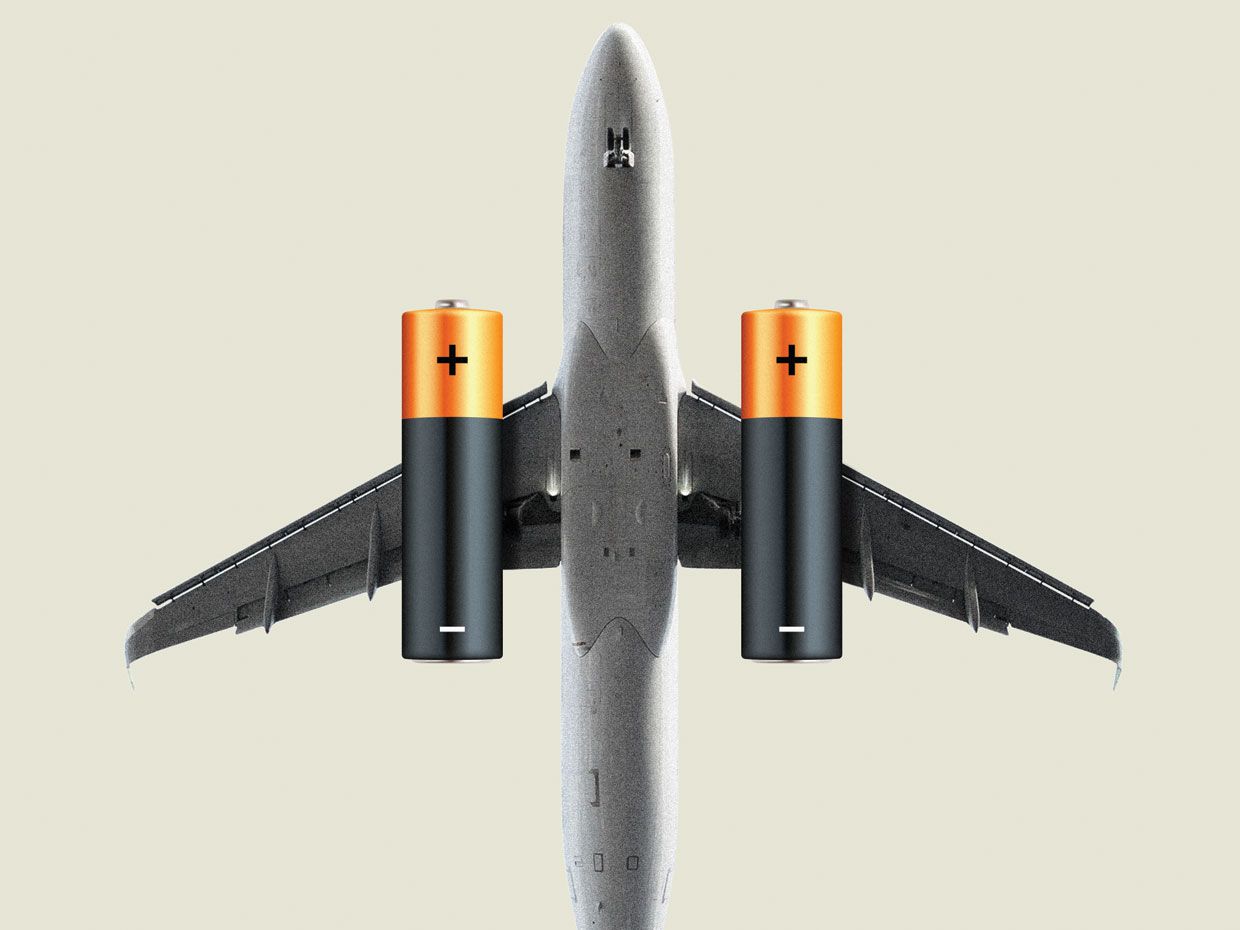
Elektroflugzeuge sind der letzte Schrei, mit Prototypen in der Entwicklung in jeder Größe von Lieferdrohnen bis hin zu Passagierflugzeugen. Aber die Technologie muss noch abheben, und das aus einem Grund: Mangel an einer geeigneten Batterie.Damit ein großes Passagierflugzeug hunderte Kilometer entfernt starten, kreuzen und landen kann, wären Batterien erforderlich, die tausende Kilogramm wiegen — viel zu schwer, als dass das Flugzeug überhaupt in die Luft steigen könnte. Selbst für relativ kleine Flugzeuge wie zweisitzige Trainer begrenzt das schiere Gewicht der Batterien die Nutzlast des Flugzeugs, schränkt seine Reichweite ein und schränkt somit ein, wo das Flugzeug fliegen kann. Die Reduzierung des Batteriegewichts wäre nicht nur für die Luftfahrt von Vorteil, sondern auch für andere Elektrofahrzeuge wie Autos, Lastwagen, Busse und Boote, deren Leistung ebenfalls direkt mit dem Energie-Gewichts-Verhältnis ihrer Batterien zusammenhängt.
Für solche Anwendungen ist die heutige Batterie der Wahl Lithium-Ionen. Es erreichte die Reife vor Jahren, mit jeder neuen inkrementellen Verbesserung kleiner als die letzte. Wir brauchen eine neue Chemie.
Seit 2004 arbeitet meine Firma Oxis Energy in Oxfordshire, England, an einem der führenden Konkurrenten — Lithium-Schwefel. Unsere Batterietechnologie ist extrem leicht: Unsere neuesten Modelle erreichen mehr als die doppelte Energiedichte, die für Lithium-Ionen-Batterien typisch ist. Lithiumschwefel ist auch in der Lage, die für die Luftfahrt erforderliche Leistung und Haltbarkeit bereitzustellen, und vor allem ist es sicher genug. Schließlich kann ein Flugzeug ein plötzliches Feuer oder eine andere Katastrophe nicht bewältigen, indem es einfach an den Straßenrand zieht.
Die neue Technologie hat lange auf sich warten lassen, aber das Warten hat nun ein Ende. Die ersten Flugversuche sind bereits abgeschlossen.
Grundsätzlich besteht eine Lithium-Schwefel-Zelle aus vier Komponenten:
- Die positive Elektrode, die sogenannte Kathode, absorbiert Elektronen während der Entladung. Es ist mit einem Stromabnehmer aus Aluminiumfolie verbunden, der mit einer Mischung aus Kohlenstoff und Schwefel beschichtet ist. Schwefel ist das aktive Material, das an den elektrochemischen Reaktionen teilnimmt. Aber es ist ein elektrischer Isolator, also liefert Kohlenstoff, ein Leiter, Elektronen dorthin, wo sie benötigt werden. Es wird auch eine kleine Menge Bindemittel zugesetzt, um sicherzustellen, dass Kohlenstoff und Schwefel in der Kathode zusammenhalten.
- Die negative Elektrode oder Anode setzt während der Entladung Elektronen frei. Es ist mit reiner Lithiumfolie verbunden. Das Lithium wirkt auch als Stromabnehmer, aber es ist auch ein aktives Material, das an der elektrochemischen Reaktion teilnimmt.
- Ein poröser Separator verhindert, dass sich die beiden Elektroden berühren und einen Kurzschluss verursachen. Der Separator wird in einen lithiumsalzhaltigen Elektrolyten gebadet.
- Ein Elektrolyt erleichtert die elektrochemische Reaktion, indem er die Bewegung von Ionen zwischen den beiden Elektroden ermöglicht.
Diese Komponenten werden verbunden und in Folie als Pouchzelle verpackt. Die Zellen sind wiederum miteinander verbunden — sowohl in Reihe als auch parallel – und verpackt in einem 20 Amperestunden, 2,15-Volt-Akku. Für ein großes Fahrzeug wie ein Flugzeug werden Dutzende von Packs verbunden, um eine Batterie zu schaffen, die Dutzende oder Hunderte von Amperestunden bei mehreren hundert Volt liefern kann.Lithium-Schwefel-Batterien sind ungewöhnlich, weil sie beim Entladen mehrere Stufen durchlaufen und jedes Mal eine andere, unterschiedliche molekulare Spezies von Lithium und Schwefel bilden. Wenn sich eine Zelle entlädt, wandern Lithiumionen im Elektrolyten zur Kathode, wo sie sich mit Schwefel und Elektronen zu einem Polysulfid, Li2S8, verbinden. An der Anode geben Lithiummoleküle Elektronen ab, um positiv geladene Lithiumionen zu bilden; Diese freigesetzten Elektronen bewegen sich dann durch den externen Stromkreis — die Last —, der sie zur Kathode zurückführt. Im Elektrolyten reagiert das neu produzierte Li2S8 sofort mit mehr Lithiumionen und mehr Elektronen zu einem neuen Polysulfid, Li2S6. Der Prozess geht weiter, Schritt durch weitere Polysulfide, Li2S4 und Li2S2, um schließlich Li2S zu werden. Bei jedem Schritt wird mehr Energie abgegeben und an die Last weitergegeben, bis die Zelle schließlich an Energie erschöpft ist.Das Wiederaufladen kehrt die Sequenz um: Ein angelegter Strom zwingt Elektronen, in die entgegengesetzte Richtung zu fließen, wodurch die Schwefelelektrode oder Kathode Elektronen abgibt und LI2S in LI2S2 umwandelt. Das Polysulfid fügt weiterhin Schritt für Schritt Schwefelatome hinzu, bis Li2S8 in der Kathode erzeugt wird. Und jedes Mal, wenn Elektronen abgegeben werden, werden Lithiumionen erzeugt, die dann durch den Elektrolyten diffundieren und sich mit Elektronen an der Lithiumelektrode zu Lithiummetall verbinden. Wenn alle Li2S in Li2S8 umgewandelt wurden, ist die Zelle vollständig geladen.
Diese Beschreibung ist vereinfacht. In Wirklichkeit sind die Reaktionen komplexer und zahlreicher und finden auch im Elektrolyten und an der Anode statt. Tatsächlich sind es über viele Lade- und Entladezyklen diese Nebenreaktionen, die in einer Lithium-Schwefel-Zelle zu einem Abbau führen. Diese zu minimieren, durch die Auswahl der geeigneten Materialien und Zellkonfiguration, ist die grundlegende, zugrunde liegende Herausforderung, die erfüllt werden muss, um eine effiziente Zelle mit einer langen Lebensdauer zu produzieren.Eine große Herausforderung für Lithium-Ionen- und Lithium-Schwefel-Technologien war die Tendenz, dass wiederholte Lade- und Entladezyklen die Anode verschlechtern. Im Falle von Lithiumionen passen sich Ionen, die an dieser Elektrode ankommen, normalerweise in Zwischenräume im Metall ein, ein Prozess, der als Interkalation bezeichnet wird. Aber manchmal plattieren Ionen die Oberfläche und bilden einen Kern, auf dem sich weitere Ablagerungen ansammeln können. Über viele Zyklen kann ein Filament oder Dendrit wachsen, bis es die gegenüberliegende Elektrode erreicht und die Zelle kurzschließt, was einen Energieschub in Form von Wärme verursacht, der die Zelle irreparabel schädigt. Wenn eine Zelle so zusammenbricht, kann sie eine benachbarte Zelle dazu veranlassen, dasselbe zu tun, was einen Dominoeffekt auslöst, der als thermische Ausreißerreaktion bekannt ist — im allgemeinen Sprachgebrauch ein Feuer.
Bei Lithium-Schwefel-Zellen ist auch der Abbau der Lithium-Metall-Anode ein Problem. Dies geschieht jedoch über einen ganz anderen Mechanismus, der nicht die Bildung von Dendriten beinhaltet. In Lithium-Schwefel-Zellen führen ungleichmäßige Stromdichten auf der Anodenoberfläche dazu, dass Lithium beim Laden und Entladen der Batterie ungleichmäßig plattiert und abgestreift wird. Im Laufe der Zeit verursacht diese ungleichmäßige Beschichtung und Ablösung moosartige Ablagerungen auf der Anode, die mit dem Sulfid und den Polysulfiden im Elektrolyten reagieren. Diese moosartigen Ablagerungen werden elektrisch von der Massenanode getrennt, so dass weniger von der Anodenoberfläche für chemische Reaktionen zur Verfügung steht. Schließlich, wenn dieser Abbau fortschreitet, kann die Anode nicht mehr funktionieren und verhindert, dass die Zelle Ladung annimmt.
Die Entwicklung von Lösungen für dieses Degradationsproblem ist entscheidend für die Herstellung einer Zelle, die über viele Lade-Entlade-Zyklen auf hohem Niveau arbeiten kann. Eine vielversprechende Strategie, die wir bei Oxis verfolgt haben, besteht darin, die Lithium-Metall-Anode mit dünnen Schichten keramischer Materialien zu beschichten, um eine Degradation zu verhindern. Solche keramischen Materialien müssen eine hohe Ionenleitfähigkeit aufweisen und elektrisch isolierend sowie mechanisch und chemisch robust sein. Die keramischen Schichten lassen Lithiumionen ungehindert passieren und werden in das darunter liegende Lithiummetall eingebaut.
Wir arbeiten an der Schutzschicht für die Anode in Zusammenarbeit mit Pulsedeon und Leitat und sind optimistisch, dass dadurch die Anzahl der Entlade- und Ladevorgänge einer Zelle drastisch erhöht wird. Und es ist nicht unsere einzige Partnerschaft. Wir arbeiten auch mit Arkema zusammen, um die Kathode zu verbessern, um die Leistung und Energiedichte der Batterie zu erhöhen.In der Tat ist der Hauptvorteil von Lithium-Ionen-Batterien gegenüber ihren Vorgängern – und von Lithium-Schwefel gegenüber Lithium-Ionen – die große Menge an Energie, die die Zellen in eine kleine Menge an Masse packen können. Die Blei-Säure-Starterbatterie, die den Verbrennungsmotor in einem Auto antreibt, kann etwa 50 Wattstunden pro Kilogramm speichern. Typische Lithium-Ionen-Designs können zwischen 100 und 265 Wh / kg halten, abhängig von den anderen Leistungsmerkmalen, für die sie optimiert wurden, wie Spitzenleistung oder lange Lebensdauer. Oxis hat kürzlich einen Prototyp einer Lithium-Schwefel-Pouch-Zelle entwickelt, die sich als fähig für 470 Wh / kg erwiesen hat, und wir erwarten, innerhalb eines Jahres 500 Wh / kg zu erreichen. Und weil die Technologie noch neu ist und Raum für Verbesserungen bietet, ist es nicht unvernünftig, bis 2025 mit 600 Wh / kg zu rechnen.
Wenn Zellhersteller Energiedichtewerte angeben, geben sie normalerweise die Energie an, die verfügbar ist, wenn die Zelle mit konstanten, niedrigen Leistungsraten entladen wird. In einigen Anwendungen sind solche niedrigen Raten in Ordnung, aber für die vielen vorgesehenen elektrischen Flugzeuge, die vertikal abheben, muss die Energie mit höheren Leistungsraten geliefert werden. Ein solches Hochleistungsmerkmal muss gegen eine geringere Gesamtenergiespeicherkapazität eingetauscht werden.
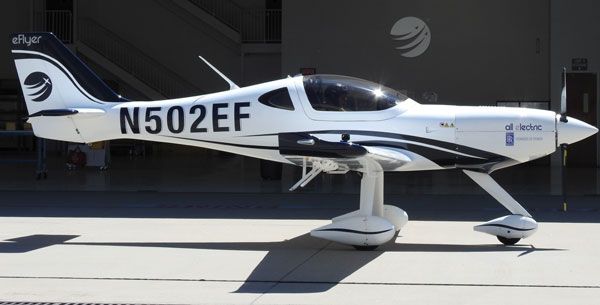
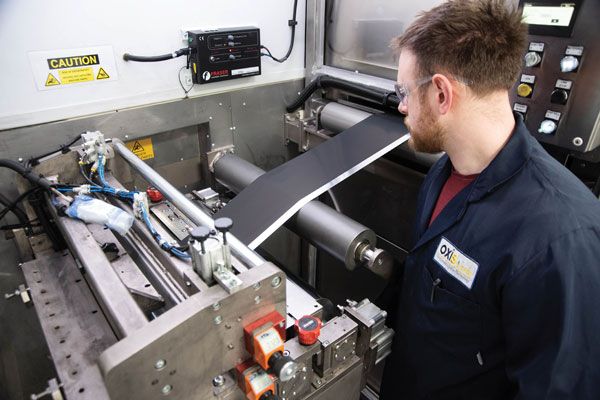
Darüber hinaus kann die in einer einzelnen Zelle erreichbare Energiedichte erheblich höher sein als in einer Batterie, die aus vielen solcher Zellen besteht. Die Energiedichte überträgt sich nicht direkt von der Zelle auf die Batterie, da Zellen eine Verpackung benötigen — das Gehäuse, das Batteriemanagementsystem und die Anschlüsse und möglicherweise Kühlsysteme. Das Gewicht muss in Schach gehalten werden, und aus diesem Grund verwendet unser Unternehmen fortschrittliche Verbundwerkstoffe, um leichte, starke und druckfeste Gehäuse zu entwickeln.
Wenn die Verpackung richtig gemacht wird, kann die Energiedichte der Batterie auf 80 Prozent der der Zellen gehalten werden: Eine Zelle mit einem Nennwert von 450 Wh / kg kann mit mehr als 360 Wh / kg in der endgültigen Batterie verpackt werden. Wir erwarten, dass wir es besser machen, indem wir die Batterie in das Flugzeug integrieren, zum Beispiel, indem wir den Flügelraum doppelt so beanspruchen wie das Batteriegehäuse. Wir gehen davon aus, dass die Zahl dadurch auf 90 Prozent steigen wird.
Um die Batterieleistung zu optimieren, ohne die Sicherheit zu beeinträchtigen, setzen wir in erster Linie auf ein Batteriemanagementsystem (BMS), eine Kombination aus Software und Hardware, die die Batterie steuert und schützt. Es enthält auch Algorithmen zur Messung der in einer Batterie verbleibenden Energie und andere zur Minimierung der während des Ladevorgangs verschwendeten Energie.Wie Lithium-Ionen-Zellen unterscheiden sich Lithium-Schwefel-Zellen geringfügig voneinander. Diese Unterschiede sowie Unterschiede in der Position der Zellen im Akkupack können dazu führen, dass einige Zellen konstant heißer laufen als andere. Im Laufe der Zeit verschlechtern diese hohen Temperaturen langsam die Leistung, daher ist es wichtig, die Leistungsunterschiede von Zelle zu Zelle zu minimieren. Dies wird in der Regel mit einer einfachen Balancing-Lösung erreicht, bei der mehrere Widerstände parallel zu einer Zelle geschaltet werden, die alle durch Software im BMS gesteuert werden.
Selbst wenn die Lade- und Entladeraten innerhalb sicherer Grenzen gehalten werden, kann jede Batterie immer noch übermäßige Wärme erzeugen. Daher ist in der Regel ein dediziertes Wärmemanagementsystem erforderlich. Ein Elektroauto kann Flüssigkeitskühlung verwenden, aber in der Luftfahrt wird Luftkühlung viel bevorzugt, weil sie weniger Gewicht hinzufügt. Natürlich kann die Batterie an einem Punkt platziert werden, an dem sich Luft auf natürliche Weise über die Oberfläche des Flugzeugs bewegt — möglicherweise über den Flügel. Bei Bedarf kann Luft durch Kanäle zur Batterie geleitet werden. Bei Oxis verwenden wir Computermodellierung, um diese Kühlung zu optimieren. Als wir diese Technik beispielsweise in einem Projekt für ein kleines Starrflügelflugzeug eingeführt haben, konnten wir ein effektives Wärmemanagementsystem entwickeln, ohne das die Batterie ihre Temperaturgrenzen erreichen würde, bevor sie vollständig entladen ist.
Wie oben erwähnt, ist ein Batteriepack typischerweise mit den Zellen sowohl parallel als auch in Reihe angeordnet. Die Anordnung der Zellen hat jedoch noch mehr zu bieten. Natürlich ist die Batterie eine unternehmenskritische Komponente eines E-Flugzeugs, daher möchten Sie Redundanz für mehr Sicherheit. Sie könnten zum Beispiel die Batterie in zwei gleichen Teilen entwerfen, so dass, wenn eine Hälfte ausfällt, kann es getrennt werden, so dass das Flugzeug mit mindestens genug Energie, um einen kontrollierten Abstieg und Landung zu verwalten.
Eine weitere Softwarekomponente innerhalb des BMS ist der Ladezustandsalgorithmus. Stellen Sie sich vor, Sie müssten ein Auto fahren, dessen Tankanzeige einen Messfehler von 25 Prozent des Tankvolumens aufwies. Sie würden den Indikator niemals auf 25 Prozent fallen lassen, nur um sicherzustellen, dass das Auto nicht zum Stillstand kommt. Ihre praktische Reichweite würde nur drei Viertel der tatsächlichen Reichweite des Autos betragen. Um solche Verschwendung zu vermeiden, hat Oxis großen Wert auf die Entwicklung modernster Algorithmen gelegt.
In einer Lithium-Ionen-Batterie können Sie die Ladung abschätzen, indem Sie einfach die Spannung messen, die mit dem Energieniveau abfällt. Aber es ist nicht so einfach für eine Lithium-Schwefel-Batterie. Denken Sie daran, dass in der Lithium-Schwefel-Batterie verschiedene Polysulfide zu unterschiedlichen Zeiten während des Ladens und Entladens am elektrochemischen Prozess beteiligt sind. Das Ergebnis ist, dass die Spannung kein guter Indikator für den Ladezustand ist und, um die Sache noch komplizierter zu machen, die Spannungskurve für Ladung und Entladung asymmetrisch ist. Die Algorithmen, die benötigt werden, um den Ladezustand zu verfolgen, sind also viel ausgefeilter. Wir haben unsere mit der Cranfield University in England unter Verwendung statistischer Techniken, darunter des Kalman-Filters, sowie neuronaler Netze entwickelt. Wir können den Ladezustand mit einer Genauigkeit von wenigen Prozent abschätzen, und wir arbeiten daran, es noch besser zu machen.
Alle diese Designentscheidungen beinhalten Kompromisse, die für verschiedene Flugzeuge unterschiedlich sind. Wir variieren, wie wir diese Kompromisse handhaben, um unsere Batteriedesigns für drei verschiedene Flugzeugtypen anzupassen.
- High-Altitude Pseudo Satellites (HAPS) sind Flugzeuge, die in etwa 15.000 bis 20.000 Metern Höhe fliegen. Die Hoffnung ist, monatelang fliegen zu können; Der aktuelle Rekord liegt bei 26 Tagen und wurde 2018 vom Airbus Zephyr S aufgestellt. Da die 24-stündige Lade- und Entladezeit nur wenig Strom benötigt, können Sie eine leichte Batterie konstruieren und so eine große Nutzlast zulassen. Die Leichtigkeit erleichtert es einem solchen Flugzeug auch, weit vom Äquator entfernt zu fliegen, wo die Nacht länger dauert.
- eVTOL-Flugzeuge (Electric Vertical Take-off and Landing) werden als fliegende Taxis entwickelt. Unter anderem Lilium in Deutschland und Uber Elevate haben bereits solche Projekte im Gange. Auch hier ist das Gewicht entscheidend, aber hier müssen die Batterien nicht nur leicht, sondern auch leistungsstark sein. Oxis hat daher zwei Versionen seiner Zellchemie entwickelt. Die Hochenergieversion ist in vielen Aspekten des Zellendesigns optimiert, um das Gewicht zu minimieren, ist jedoch auf relativ geringe Leistung beschränkt. Es ist am besten für HAPS-Anwendungen geeignet. Die Hochleistungsversion wiegt mehr, wenn auch immer noch deutlich weniger als eine Lithium-Ionen-Batterie vergleichbarer Leistung; es ist gut geeignet für Anwendungen wie eVTOL.
- Leichte Starrflügler: Die steigende Nachfrage nach Piloten trifft auf die hohen Ausbildungskosten; ein vollelektrisches Trainerflugzeug würde die Betriebskosten drastisch senken. Ein Schlüsselfaktor ist die längere Flugdauer, die durch die leichtere Batterie ermöglicht wird. Bye Aerospace in Colorado ist ein Unternehmen, das bei solchen Flugzeugen führend ist. Darüber hinaus planen andere Unternehmen — wie easyJet, eine Partnerschaft mit Wright Electric — vollelektrische kommerzielle Passagierjets für Kurzstreckenflüge von 2 Stunden.
Drei Faktoren bestimmen, ob Lithium-Schwefel-Batterien letztendlich erfolgreich sind oder nicht. Erstens ist die erfolgreiche Integration der Batterien in mehrere Flugzeugtypen, um das Prinzip zu beweisen. Zweitens ist die kontinuierliche Verfeinerung der Zellchemie. Drittens ist die kontinuierliche Reduzierung der Stückkosten. Ein Plus hier ist, dass Schwefel ungefähr so billig ist, wie Materialien bekommen, also gibt es Grund zu hoffen, dass mit der Volumenfertigung die Stückkosten unter die des Lithium-Ionen-Designs fallen werden, wie es für den kommerziellen Erfolg erforderlich wäre.
Oxis hat bereits zehntausende Zellen produziert und führt derzeit zwei neue Projekte durch. Derzeit wird in Port Talbot, Wales, eine Produktionsanlage zur Herstellung sowohl des Elektrolyten als auch des kathodenaktiven Materials errichtet. Später wird die eigentliche Massenproduktion von Lithium-Schwefel-Zellen an einem Standort von Mercedes-Benz Brasilien im brasilianischen Minas Gerais beginnen.
Diese hochmoderne Anlage soll bis 2023 in Betrieb genommen werden. Wenn sich die Skaleneffekte bewähren und die Nachfrage nach Elektroflugzeugen wie erwartet steigt, könnten Lithium-Schwefel-Batterien beginnen, Lithium-Ionen-Batterien in diesem Bereich zu ersetzen. Was in der Luft funktioniert, muss auch am Boden funktionieren.
Dieser Artikel erscheint in der Printausgabe August 2020 als „Ultralight Batteries for Electric Airplanes.“
Über den Autor
Mark Crittenden ist Leiter der Batterieentwicklung und -integration bei Oxis Energy in Oxfordshire, Großbritannien